Экстренный переход от импортных комплектующих для кабины грузовиков К5 к антисанкционному производству потребовал мобилизации усилий не только от камазовцев, но и от многих российских предприятий - поставщиков автогиганта. "Вести КАМАЗа" уже предлагали интервью о том, как локализация отразилась на работе ПРЗ в Набережных Челнах, теперь же об организации системной работы с поставщиками рассказывает руководитель проекта «Аутсорсинг производства "КАМАЗа"» Сергей Мандрик.
ВЫШЛИ НА 115 ЗАВОДОВ, ОТОБРАЛИ 24
– Сергей Викторович, как сформировалась группа для работы с аутсорсерами и какие задачи ставились перед вами на первом этапе?
– Нашей целью была поставка на конвейер 135 наименований комплектующих, и сделать это требовалось в максимально короткие сроки. В перечень были включены климатическая система, элементы обивки, термошумоизоляция, воздухозаборник, фильтры, сложные литые кронштейны, замки, заглушки, уплотнители, причем каждая деталь со своими особенностями. Семейства изделий были распределены среди сотрудников небольшой группы из восьми человек. Она включала специалистов по технологии машинных производств, закупкам, логистике, бережливому производству. Каждый из них отвечал за освоение порученных изделий, изучал технологию их производства и разбирался в нюансах функционирования.
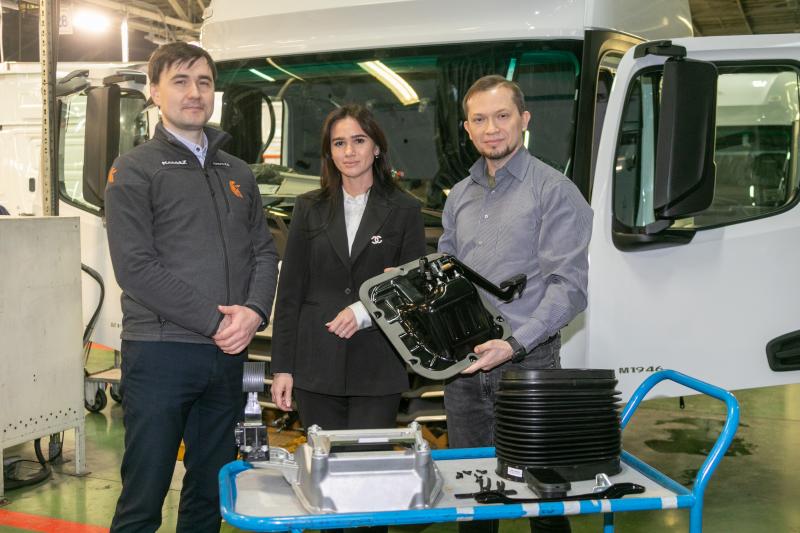
Участники проекта Евгений Герило, Алсу Гараева и Александр Петухов
– Сколько российских предприятий попало в поле зрения команды?
– К сотрудничеству мы изначально пригласили 115 предприятий, но после тщательного отсева поставщиками стали 24 из них. Чтобы определиться с партнерами, мы сначала передали им 3D-модели требуемых изделий и пригласили на "КАМАЗ". Их технологи и конструкторы вживую увидели, как детали функционируют в составе автомобиля, получили возможность согласовать со специалистами НТЦ отдельные конструктивные изменения. Затем мы собрали коммерческие предложения, отобрали подходящие, и утвержденные поставщики начали готовить свои производства. Мы получали от них первые изделия для пробных сборок и ждали первых опытно-промышленных партий с измененными конструкциями. Итоговый вид изделий во многом определили представители технологической службы АвЗ и департамента качества. Тем временем центр закупок заключал договора на серийные поставки. В целом локализация комплектующих заняла около года.
– Поставщики осваивали технологии с нуля?
– Такие примеры были, приведу один из них. Прежде мы закупали в Германии смолонаполненную базальтовую вату – основу термошумоизоляционных матов для К5. Чтобы компенсировать импорт, нам пришлось запустить НИОКР в сотрудничестве сразу с несколькими предприятиями. Сначала вышли на компанию, которая добывает базальт, крошит его, плавит и растягивает в волокна. Затем решили задачу насыщения базальта поликонденсационной смолой с сохранением однородной структуры. В итоге за год мы получили новый для отечественного рынка материал.
ПОД РОСТ ПРОИЗВОДСТВА У ПОСТАВЩИКОВ ЕСТЬ РЕЗЕРВ
– Наверное, была номенклатура, которая не требовала больших усилий?
– Быстрее всего на конвейер стали поступать заглушки и мелкий крепеж - дюбеля, фиксаторы, клипсы, кнопки… Но даже их производство имеет свои секреты, а их несвоевременная поставка способна остановить ГСК так же, как и самая значимая деталь. В освоении узлов очень много нюансов. Взять хотя бы петлю крепления дверцы вещевого ящика: она требует штамповки, клепки, алюминиевого литья и литья пластиков, при этом качество итоговой сборки должно быть на уровне.
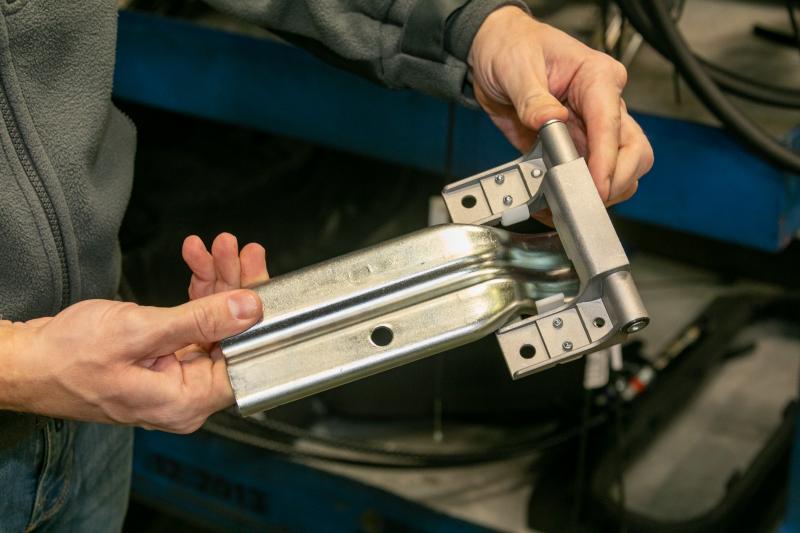
– Поставщики не подводили в вопросах качества?
– Все наши российские поставщики знают требования компании и стремятся им соответствовать. Они понимают, что сегодня освоение нового продукта и обеспечение стабильного качества – это единственный путь к развитию, возможность застолбить место на изменчивом рынке. Вопросы технологического и конструкторского характера, конечно, возникали, но все они были успешно разрешены.
– Программу локализации можно считать закрытой?
– Не вполне: остается еще одна деталь - алюминиевый кронштейн колонки рулевого управления. С его исполнением мы определились совсем недавно, это очень сложное, ажурное, тонкостенное литое изделие с особыми требованиями к конструкции. Пришлось обойти немало поставщиков и даже привлечь экспертов по литью из других стран для сравнительного анализа. В конце концов мы увидели, что и в России достаточно опытных специалистов по этому вопросу. Сейчас поставщик из Санкт-Петербурга завершает технологическую подготовку производства, и, по расчетам, к концу второго квартала этот кронштейн тоже станет полностью российским.
– Производство большегрузов класса К5 будет расти. Мощности поставщиков рассчитаны на это?
– Их резерва хватит, мы ведь учитывали мощности производства при отборе контрагентов.
Текст: Татьяна Белоножкина
Фото: Виталий Зудин
работал по двум проектам, очень сильная команда. молодцы! так держать!
Ответить (0)Удачи вам Сергей Викторович в локализации, уверен вы справитесь со всем задуманным!
Ответить (0)