Одним из главных успехов ПАО "КАМАЗ" за прошлый год стал возврат к серийному производству большегрузов поколения К5. Модель 54901 удалось пересобрать на полностью антисанкционной базе и до конца года выпустить свыше 5 тыс. тягачей. При этом проект «Локализация штампованных деталей кабины К5. Фаза 2» основательно изменил ландшафт цехов прессово-рамного завода. В интервью "Вестям КАМАЗа" руководитель проекта Антон Крюков подвел предварительные итоги обширной работы.
К КОНЦУ ГОДА ПРОИЗВОДСТВО КАРКАСОВ КАБИН БУДЕТ МАСШТАБИРОВАНО
– Антон Евгеньевич, "КАМАЗ" занялся локализацией каркаса кабины сразу после выхода на рынок тягача 54901. Каковы результаты первого этапа этой работы?
– Еще в 2016 году группа во главе с руководителем проекта Ильдаром Гараевым определила перечень из 186 деталей и узлов, которые нужно было освоить. "КАМАЗ" отдал заказ на 332 штампа одному из своих поставщиков, другая часть комплектующих к тому времени уже выпускалась на ПРЗ. В совокупности они обеспечили 71% локализации.
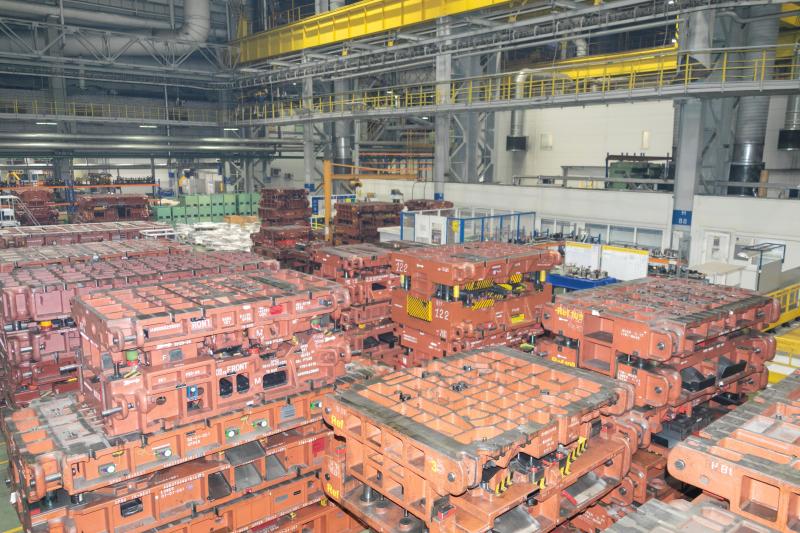
– С какими сложностями вы столкнулись во второй фазе проекта?
– Нам важно было нивелировать усиление санкций и уход с наших площадок зарубежных партнеров. Нужно было быстро изготовить 200 штампов, освоить выпуск 117 деталей в Набережных Челнах на ПРЗ и еще 23 деталей на стороннем предприятии. Самым значимым стоп-фактором стал для нас выпуск лонжеронов – эти силовые элементы обеспечивают надежность кабины. Daimler делал их методом горячей листовой штамповки. На тот момент этот способ считался ноу-хау мирового уровня, в России таких технологий не было. Наша команда решила задачу вместе со специалистами блока развития, представителями Магнитогорского металлургического комбината и поставщиками. В итоге мы получили лонжероны при помощи экономичной холодной листовой штамповки с применением перспективной двухфазной стали, и по результатам сначала вибрационного, а потом и краш-теста наш продукт показал столь же высокие характеристики, как деталь от Daimler.
– Завод был готов к росту загрузки?
– Пришлось подготовить. В цехе штамповки и сварки деталей кабин была освобождена площадка под штампы, в цехе крупной штамповки модернизирован пресс – он должен был сбалансировать нагрузку на оборудование под рост выпуска. На РИЗе мы заказали временную оснастку для изготовления узлов со сваренными деталями. В результате были созданы условия для производства 10 тысяч каркасов кабин в 2024–2025 годах.
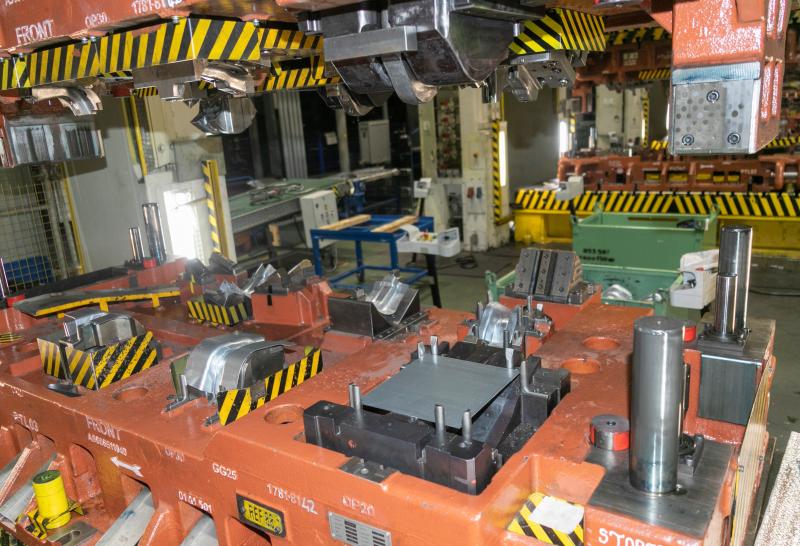
– Поскольку К5 станет основной линейкой в ассортименте "КАМАЗа", объем производства будет расти и дальше. Этот участок придется расширять еще?
– Для загрузки заготовительного производства ПРЗ уже закупается дополнительная линия продольной резки рулонов металла. В феврале начнем готовить площадку для нее. Для поперечной резки листовых заготовок достаточно модернизировать нашу нынешнюю линию. Обе они должны быть запущены до конца года. Кроме того, мы модернизируем восемь машин для рельефной сварки – добавим в систему управления защиту от ошибок. Для сборки каркаса кабины нужны 17 сваренных узлов, которые сейчас изготавливаются на временной оснастке. При увеличении объемов на смену ей придет роботизированная сварочная ячейка, уже испытанная у поставщика. Скоро она приедет на ПРЗ. Склад для хранения комплектующих и продукции тоже ждет модернизация. Все перечисленное должно заработать в течение года при финансовой поддержке Фонда развития промышленности.
НОВЫЕ КАБИНЫ – НОВЫЕ КОМПЕТЕНЦИИ
– Альтернативные комплектующие для каркасов кабин полностью соответствуют требованиям?
– Геометрия сваренных на ПРЗ каркасов регулярно проверяется лабораторией ATOS. Они целиком отвечают всем европейским стандартам.
– Этот проект, должно быть, заодно позволил камазовцам повысить свою квалификацию?
– Да, он позволил освоить кое-какие новые операции. Работники научились варить узлы с жесткими допусками, цех штамповки и сварки близко познакомился с многооперационными штампами. Их обслуживание тоже требует высокого уровня подготовки, но на ПРЗ были опытные специалисты, которые годами следят за штамповой оснасткой – они справляются. Кроме того, мы применили новые походы к контролю геометрии деталей: сейчас сложные проверяются в лаборатории ATOS, а простые – при помощи ручной оснастки. Работая, каждый сотрудник копит и статистику, что с течением времени сказывается на скорости переналадки оборудования и, соответственно, темпе выпуска продукта.
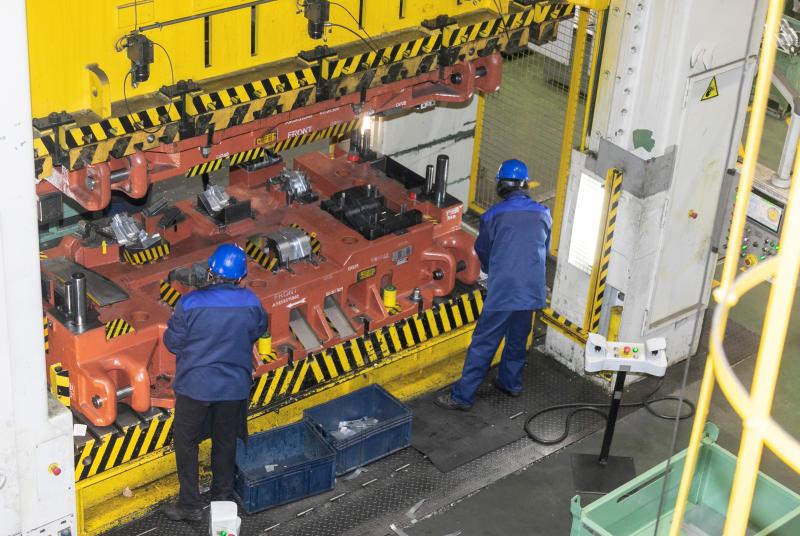
– Какие перспективы открывает перед "КАМАЗом" локализация деталей кабины?
– Цель у нас одна – "КАМАЗ" должен доминировать на рынке большегрузов. Но работа не завершена, скоро придет время осваивать новый каркас кабины класса К5. Он станет основной для кабины пожарной машины и для низко посаженной кабины городского развозного транспорта. Штамповая оснастка должна поступить на ПРЗ уже этой весной. В мае начнем ее испытания, а первые образцы завод каркасов кабин планирует выпустить осенью.
Текст: Татьяна Белоножкина
Фото: Виталий Зудин