На столе в кабинете директора автомобильного завода Антона Сарайкина - план реинжиниринга агрегатного производства. Встряска, которую задал отечественному автопрому прошлый год, придала дополнительный импульс стратегическим проектам, о которых Сарайкин рассказал "Вестям КАМАЗа".
«К ОСЕНИ – 220 ГРУЗОВИКОВ В СУТКИ»
– Антон Викторович, оцените, пожалуйста, итоги работы автомобильного завода в 2022 году.
– Я бы поставил нашей команде пять с минусом. Мы завершили сложный год с хорошими показателями, но адаптироваться к ситуации следовало быстрее. В январе 2022-го с конвейера сходили по 210 автомобилей в сутки, из них 70 - поколений К5 и К4. В феврале, когда логистические цепочки сломались, пришлось активно наращивать сборку большегрузов К3, из-за чего значительно выросла и нагрузка на агрегатное производство. Резко вырос спрос на полноприводные автомобили, но рекордных результатов в этой части – то есть выпуска 105 машкомплектов в сутки – коллектив достиг только к декабрю. Из-за логистических проблем конвейеры пришлось переводить в круглосуточный режим. Теперь же перед нами стоит новая задача: к апрелю требуется увеличить темп сборки полноприводных автомобилей до 120 машкомплектов в сутки.
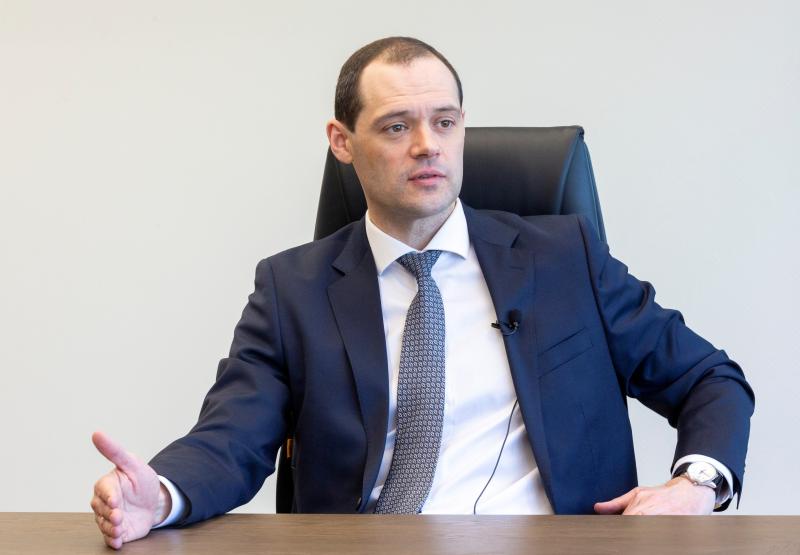
– С конвейера сошел первый локализованный магистральный тягач 54901. Нет ли сложностей с его серийной сборкой?
– Несмотря на его обновленную архитектуру, мы готовы. Практически каждый день на конвейере закладывается по 17 большегрузов этой модели, а в плане февраля значится сборка 270 автомобилей.
– Какой вклад в локализацию узлов для 54901 внесет сам завод?
– На данный момент мы уже выпускаем часть кронштейнов, трубок и других деталей для магистрального тягача, а в перспективе большегрузы класса К5 будут комплектоваться и собранными на АвЗ ведущими мостами. Проект «Мосты» прошел защиту в Фонде развития промышленности, инвестиции определены и часть оборудования под него уже контрактуется. Мы готовим линии обработки литой балки и других деталей моста, и в целом смонтируем новый сборочный конвейер, который будет оснащен умными системами контроля затяжки соединений. Добавлю, что этот проект нацелен не только на К5 – он изменит технологию производства ряда деталей и узлов для автомобилей К3. В частности, обработка таких деталей, как корпус поворотного кулака, шаровая опора, картер моста и полуось будет переведена с изношенных автоматических линий на обрабатывающие центры с ЧПУ. В планах целый цех, укомплектованный исключительно новым оборудованием. Во втором квартале начнем готовить площади под него.
– В прошлом месяце на главном конвейере собирались по 190 автомобилей в сутки. Будет ли ускоряться темп сборки и каким образом?
– Уже в этом месяце планка поднята до 200 автомобилей в сутки, в марте она должна достичь 210 единиц, а к осени – 220-ти. Конвейеры как таковые к ускорению готовы, но вопрос своевременных поставок комплектующих, включая узлы для агрегатного производства, еще не снят с повестки. Наша команда в штабном режиме отрабатывает эту тему ежедневно. К настоящему времени мы проанализировали всю цепочку изготовления мостов, балансирной подвески, раздаточных коробок, выделили отстающие от темпа звенья и разработали план действий для расшивки узких мест. Сейчас контролируем реализацию этого плана.
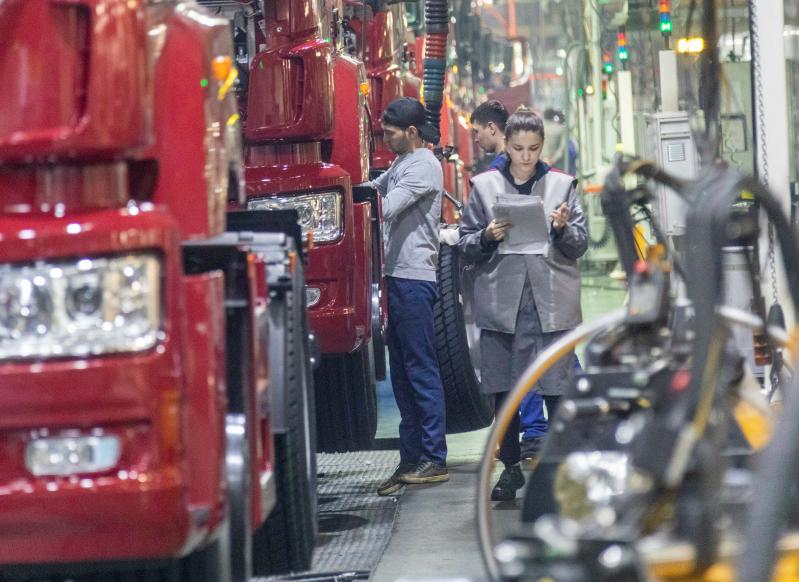
– Можете назвать болевые точки производства?
– Больше всего рекламаций мы получаем по поводу течи мостов – здесь главными факторами пока остается качество манжет и сварных соединений. Сейчас мы завершаем модернизацию автоматической сварочной линии картера моста и рассчитываем, что проблема будет решена. Кроме того, контроль качества сборки будет повышен со внедрением системы MES. Пока она работает в тестовом режиме - полномасштабный запуск пришлось перенести, потому что изменилась архитектура антисанкционного флагмана К5. Сейчас прописываются новые электронные техпроцессы для загрузки в систему, но первые плоды мы уже собираем: на каждом рабочем месте каждый рабочий обеспечен актуальной электронной инструкцией для сборки конкретного автомобиля. Инструкция визуализирована на терминале, на нем же можно моментально зарегистрировать дефект сборки и заблокировать передачу заказа на следующий участок.
РЕИНЖИНИРИНГ АГРЕГАТНОГО ПРОИЗВОДСТВА СТАРТУЕТ В 2025 ГОДУ
– В прошлом году АвЗ ввел программу стимуляции персонала для его привлечения и закрепления. Насколько эффективной она себя показала?
– Ситуация с кадрами остается напряженной как на заводе, так и в Набережных Челнах, и по всей стране. Тем не менее, весь прошлый год нам удалось отработать без привлечения на ГСК персонала из других подразделений компании. Мы опрашивали увольняющихся с автомобильного завода, и выяснили, что многих не устроил режим работы. В прошлом году нам пришлось мобилизоваться ради выполнения плана – люди работали удлиненными сменами, производство не останавливалось. Не все это выдержали, и потому сейчас одной из важнейших задач стала стабилизация режима работы.
Вторая причина – условия труда. Первое, что замечают новички – это состояние столовых, туалетов, гардеробов. За последние два года мы полностью отремонтировали 15 туалетов, в конце прошлого года начали ремонтировать гардероб в АБК-1 и после него приступим к гардеробу в АБК-2. Капитально отремонтировали кровлю. На агрегатном производстве полностью заменили освещение. Комфорт рабочего места не менее важен для выпускников колледжей, и этот вопрос решается с сокращением старых технологий - больших автоматических линий, обслуживание которых часто связано с разливами СОЖ или масел. На новом обрабатывающем центре работать гораздо удобнее, да и само по себе программирование режимов дает молодым людям новые навыки, это интересно. Благодаря этим факторам даже вопрос зарплаты отошел на третье место.
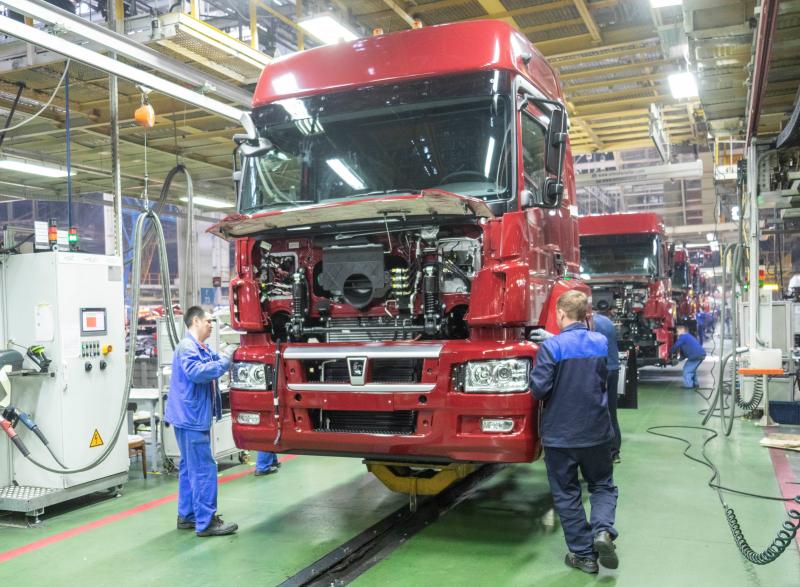
– Каким видится стратегическое развитие АвЗ?
– На сегодняшний день главным долгосрочным проектом являются «Мосты». Его необходимо завершить в 2025 году с плавным переходом к реинжинирингу агрегатного производства. Параллельно мы будем замещать громоздкие автоматические линии обрабатывающими центрами, оптимизировать производственные площади. Дорожная карта расписана до 2030 года. В перспективе модернизации ждет и конвейер сборки кабин нового модельного ряда. Сейчас он рассчитан на выпуск 20 тысяч кабин К5, но в стратегии «КАМАЗа» большегрузы нового поколения – это основная точка роста, и прирост мощностей все равно потребуется.
– Мы помним, что в четверг завод отмечает выпуск первого автомобиля. Кого планируете пригласить на праздник?
– Мы с нетерпением ждем встречи с нашими ветеранами, бывшими директорами АвЗ. Надеюсь, откликнется на приглашение и руководство «КАМАЗа». Хочется пожелать всем причастным к рождению автомобиля здоровья, каждой заводской семье – благополучия. Спасибо за терпение и понимание ситуации всем, кто продолжает трудиться в непростых условиях! Мы постараемся сохранить заводские традиции, чтобы каждый чувствовал себя на своем рабочем месте комфортно и был уверен, что любой коллега и руководитель готов подставить плечо.
Текст: Татьяна Белоножкина
Фото: Виталий Зудин
а где фото с Агрегатного завода?
Ответить (0)