На новом производстве прессово-рамного завода в тестовом режиме собрали первую партию рам для большегруза 54901. Сразу после проверки началась доводка оборудования – рабочие места на линии должны быть эргономичными и удобными.
Новый конвейер имеет необычную для сборочной линии Г-образную форму: одна часть идет параллельно линии окраски, вторая уходит в глубь производственного корпуса.
«Концепция нового конвейера отличается от существующих вариантов, – пояснил руководитель подпроекта «Производство рам» Максим Фазулин. – Дело в том, что сегодня рамы собираются из грунтованных или неокрашенных деталей. По новой технологии «хребет» будет производиться из полностью окрашенных комплектующих, что обеспечит требуемые параметры по коррозионной стойкости. Еще одно отличие линии – сборка рамы в перевернутом положении, что позволило исключить операцию кантования на 180 градусов».
В составе конвейера 10 позиций. На нулевую в автоматическом режиме краны-штабелеры подают лонжероны и усилители под план производства, тут же производится маркировка контуров деталей для помощи рабочим при установке кронштейнов. На первой позиции будет вестись подсборка лонжеронов с усилителями, на второй и третьей – формирование геометрии рамы, с четвертой по седьмую – установка кронштейнов. На предпоследней, восьмой – проверка ОТК на соответствие рамы конструкторской документации, дальше завеска на подвесной толкающий конвейер (ПТК) для их отправки на АвЗ.
Между позициями рамы будут перемещаться с помощью шатлов, движущихся по принципу челнока. Использование этого типа транспорта избавило от необходимости вести фундаментные работы, а значит, позволило сэкономить время и инвестиции.
Вдоль конвейера установлены специальные столы, куда необходимые комплектующие подаются манипуляторами с ПТК в автоматическом режиме. Для ускорения процесса сборки и помощи рабочим предусмотрена система Pick to Light. Необходимые для крепления детали будут подсвечиваться специальными лампочками. Конвейер уже оснащен гидравлическими скобами для надежной клепки, а сборка резьбовых соединений будет производиться электрогайковертами с высокой степенью точности.
Практически все оборудование смонтировано, за исключением ПТК для транспортировки рамы на АвЗ. Ведут работы представители изготовителя – НПФ «Инжер».
«Для нас линия сборки рам стала воплощением всех идей, над которыми фирма работала со дня своего основания в одном проекте», – подчеркнул директор по производству Игорь Фокин.
Сейчас как раз ведется программирование и настройка всех механизмов штабелеров, шатлов, манипуляторов, подвесной и монорельсовых систем. Кроме конвейера в комплекс оборудования включены участки завески деталей рам на окраску и подсборки поперечин, автоматизированная система транспортировки лонжеронов, транспортная система комплектующих и два автоматизированных склада окрашенных лонжеронов и деталей. Вся система должна работать четко и слаженно. При трехсменном режиме работы мощности конвейера позволяют производить 65 тыс. рам в год.
Параллельно с наладкой оборудования будет вестись тестовая сборка других типов рам. На очереди «фундамент» для КАМАЗа-65801 класса К4.
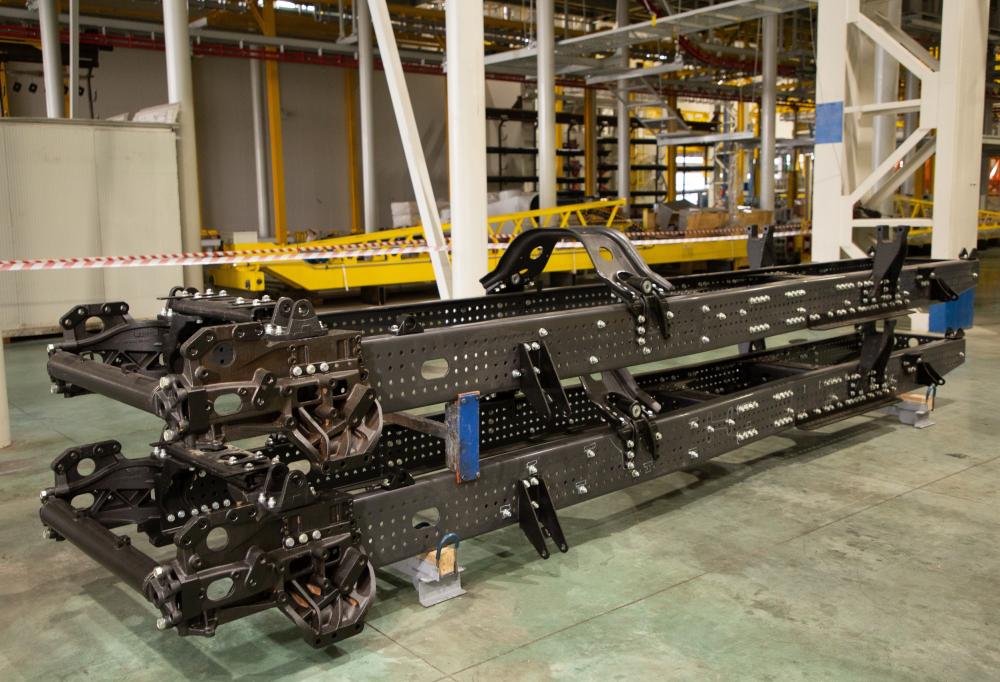
На новом конвейере собраны первые рамы для К5
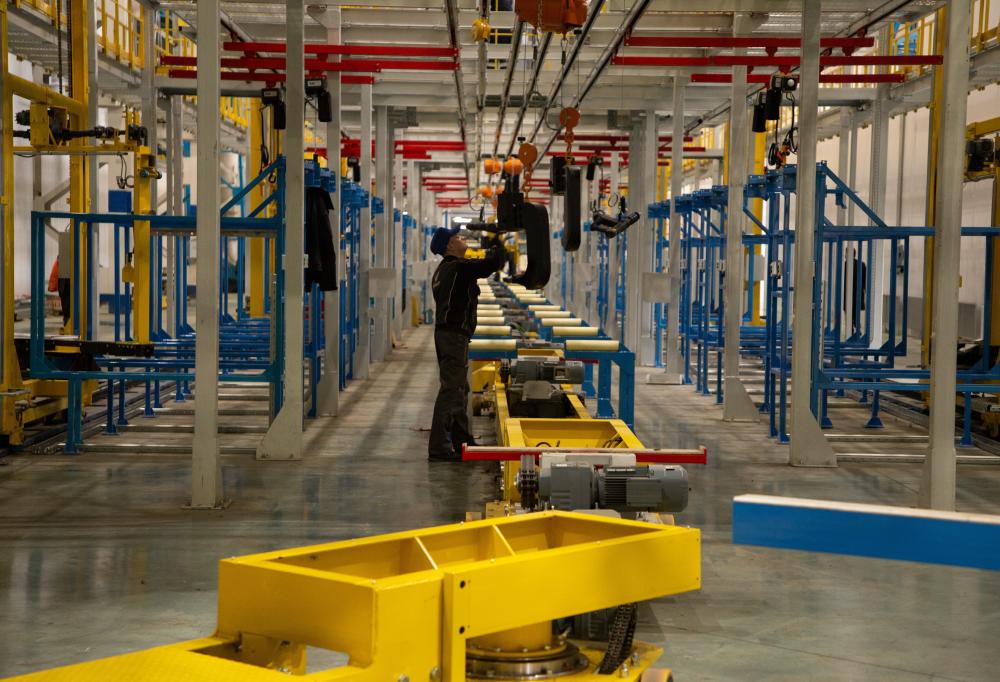
Перед запуском идет проверка инструмента и функциональных систем
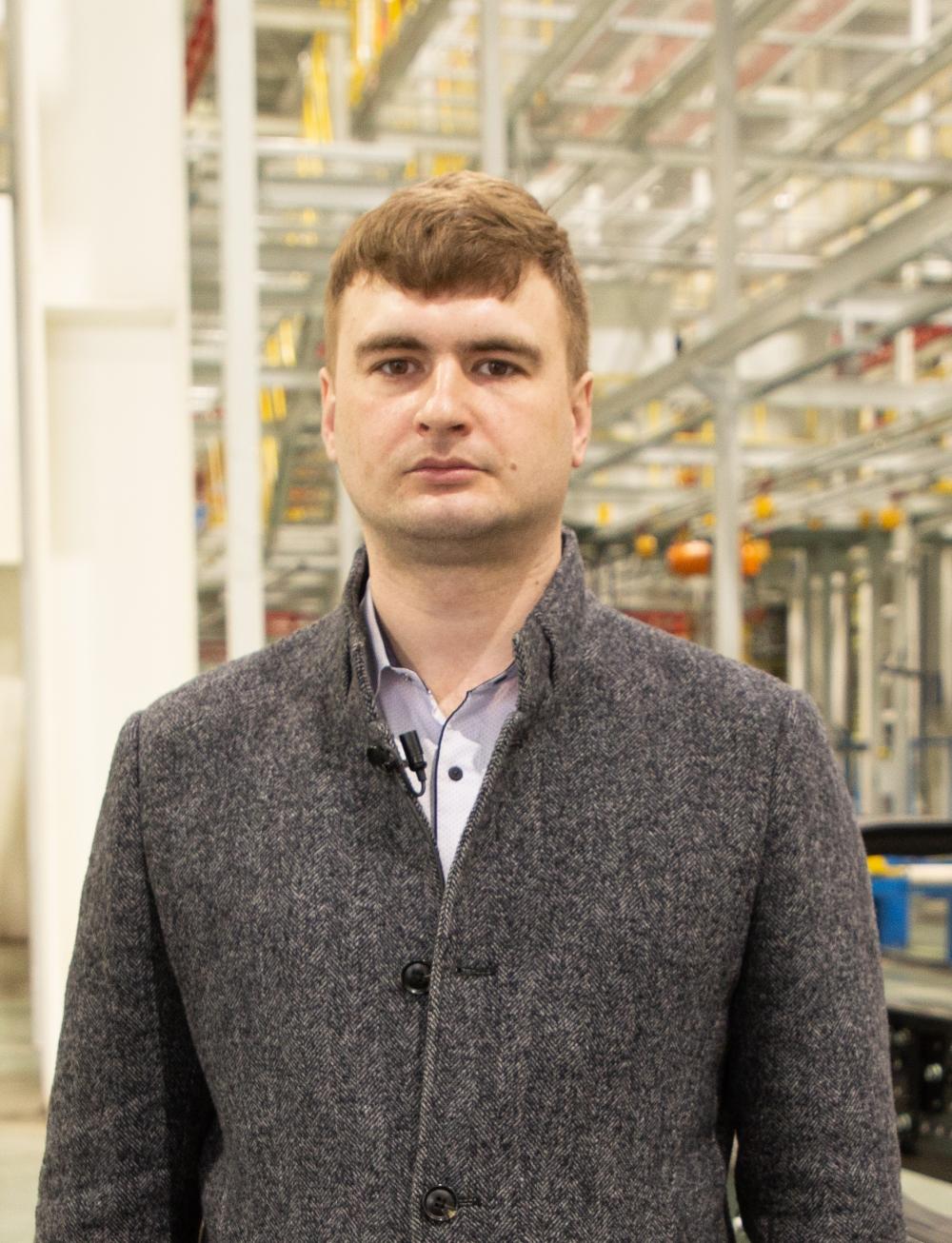
Максим Фазулин: «Уровень автоматизации логистики на этом конвейере не имеет аналогов»
О первый раз о реальном человеке из Реинжиниринга написали))) Правда ни слова про проект(((
Ответить (0)