Благодаря применению нового способа обработки зубьев зубчатых колес дисковым лезвийным инструментом отпала необходимость в закупке специального зуборезного инструмента. В ежегодном камазовском конкурсе именно эта работа, внедренная на опытно-промышленном заводе НТЦ, названа лучшим изобретением 2022 года.
«ВАЖНО ИЗГОТОВИТЬ И ИСПЫТАТЬ ПРОДУКТ В СРОК»
Авторство изобретения принадлежит группе сотрудников технологического центра: главному конструктору ТЦ Айрату Фасхутдинову, ведущему инженеру-конструктору Алексею Кондрашову и сотруднику опытно-промышленного завода НТЦ, главному технологу Артуру Мирсияпову.
Как рассказывают новаторы, они разработали и внедрили для станка с ЧПУ программу, позволяющую обрабатывать зубья зубчатых колес стандартным инструментом. Если раньше операция выполнялась специальной фрезой, то теперь – дисковым лезвийным инструментом. К изобретению, как обычно это бывает, подтолкнули обстоятельства.
«Для обработки нестандартных зубчатых венцов требуется специальный зуборезный инструмент, срок поставки которого – от 3 до 6 месяцев. В условиях современного опытного производства ожидание недопустимо, важно изготовить и испытать продукт в срок. Отсюда и возникла идея использовать дисковые и концевые фрезы на обрабатывающих центрах с ЧПУ», – поделился Фасхутдинов.
Над решением новой задачи работали в команде, потому что обработка зубчатых венцов в опытном производстве очень сложна. С одной стороны - невысокая точность оснастки, трудности измерения полуфабриката в зоне обработки; с другой – повышенная сложность зубчатых деталей. Чтобы достичь нужной точности уже на первой детали, решили измерять обработанную поверхность зуба 3D-щупом непосредственно на станке, с последующей коррекцией.
Математическим моделированием движения инструмента и заготовки занимался Кондрашов, Фасхутдинов работал над выбором схем и характеристик измерительных средств, а Мирсияпов руководил коррекцией положения инструмента и заготовки по данным автоматизированных измерений. Для Мирсияпова это изобретение первое, в то время как его коллеги – изобретатели со стажем.
«На разработку схем, математических зависимостей, программирование ушло три месяца. Еще два – на апробацию технологии. Для реализации потребовались преимущественно человеческие ресурсы, а этап апробации проводился на имеющемся оборудовании без дополнительных затрат», – поясняет Фасхутдинов.
СЭКОНОМИЛИ ВРЕМЯ И ДЕНЬГИ
Благодаря слаженной работе сроки изготовления экспериментальных образцов удалось сократить, уровень наладочного брака снизить, а экономику производства улучшить. «Кроме долгих сроков поставки специнструмент еще и дорого стоит - от 30 до 170 тысяч рублей за штуку, в зависимости от параметров и объема заказа», - поясняет Мирсияпов. Теперь, благодаря разработанной программе, от покупки специнструмента можно отказаться.
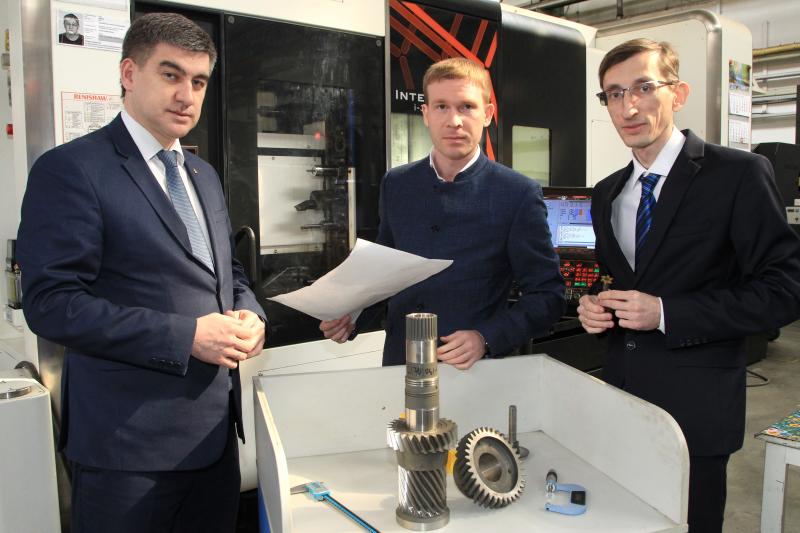
Изобретатели говорят, что материальное вознаграждение за изобретение – фактор хоть и приятный, но не главный. Для них важнее признание коллег и возможность увидеть свое детище в производстве. Инженеры планируют и дальше совершенствовать технологии как в опытном, так и в серийном производстве зубчатых колес.
Текст: Татьяна Парамонова
Фото: Александр Авдейчик
Молодца, ребята!
Ответить (0)