Поставки комплектующих со склада на производство постепенно переходят под контроль компьютера – применение системы SAP в пилотном цеху картеров уже позволило сэкономить человеческие трудозатраты и высвободить новые площади, а с августа логистический центр планирует распространить автоматизацию планирования еще на несколько цехов. О первых результатах такой автоматизации "Вестям КАМАЗа" рассказал директор ЛЦ Евгений Архипов.
«ТЕПЕРЬ ЗАКАЗ ФОРМИРУЕТСЯ БЕЗ СПЕШКИ…»
– Евгений Юрьевич, зачем понадобилось менять механизмы поставок на производство?
– Все дело в учете: чем выше точность данных, тем гибче можно выстроить поставки, а они, в свою очередь, влияют на эффективность производства. Тем более, что оптимизировать учет позволяет система SAP, нужно лишь активнее ее использовать. Этим мы и занимаемся на пилотном участке – на складе № 58966, с которого комплектующие поставляются в цех картеров автомобильного завода.
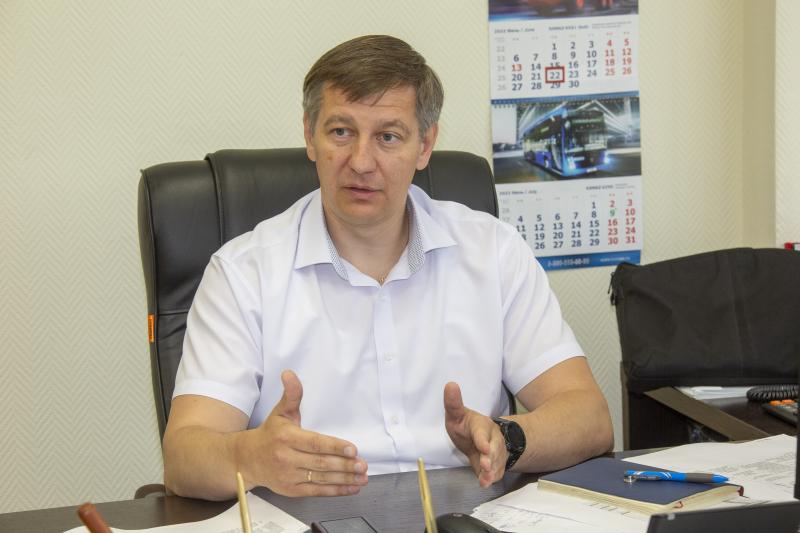
– Как изменилась схема вашего взаимодействия?
- Логистический центр в своей работе опирается на план сборки автомобилей, но зачастую производственный мастер, обходя поутру участок, не пользуется системными данными. Он смотрит, сколько заготовок для поковок и отливок еще осталось, вручную составляет заявку и отдает на склад. Склад начинает формировать заказ, а чуть погодя может поступить вторая заявка, с корректировками, и ее так же оперативно приходится отрабатывать. С пилотного участка задание для склада составляется системой в автоматическом режиме. Поставку, которая должна обеспечить сборку мостов и картеров, SAP раскидывает на узлы, подузлы и компоненты, анализирует остатки заготовок в технологической цепочке. Таким образом система формирует комплектовочную ведомость, в которой указаны позиции, их количество, а также время и последовательность их подачи в производство. С таким алгоритмом сдвинулся и горизонт планирования – теперь заказ формируется без спешки, в течение суток.
- Как долго вы тестируете этот подход и почему именно на комплектующих для цеха картеров?
- Внедрять проект начали в феврале, а пилотный участок выбирали по принципу хранения – нужен был стеллажный склад с адресными ячейками, в которых все позиции предназначены для одного цеха. На стадии подготовки логисты вместе с технологами и производственниками разработали дорожную карту. Они проанализировали технологические нормы, оптимальную загрузку автоматических линий и обрабатывающих центров, актуализировали данные по мастер-таблицам, видам упаковки, графикам поставок... На основе полученных данных в SAP были настроены параметры планирования. Поставки по ведомостям, выданным системой в автоматическом режиме, начались с 1 июня.
СЭКОНОМИЛИ ДВЕ ПАРЫ РУК, ПОДНЯЛИ ЗАРПЛАТУ
– Планирование – это хорошо, но можно ли оценить эффект от автоматизации в цифрах, в экономии времени или других ресурсов?
– Производственный мастер, к примеру, вообще больше не тратит время на заявку, а складские работники спокойно распределяют свои силы на решение разных задач вместо того, чтобы комплектовать заявку в авральном режиме. Это позволило оптимизировать численный состав складского персонала: если раньше заявки цеха обслуживали восемь человек, то теперь – шестеро, то есть на четверть меньше. Благодаря такой разгрузке у оставшихся специалистов на 15 процентов выросла зарплата. Вместе с этим комплектовщики и кладовщики освоили новую для себя профессию оператора логистических работ. Теперь каждый из них может сесть за руль ричтрака, снять груз, собрать и оформить заказ. А те двое, что высвободились со склада, на новом участке распаковывают мосты, закупленные у сторонних поставщиков. Прежде это делали слесари механосборочных работ, и на распаковку каждого моста у них уходило по 10 минут рабочего времени.
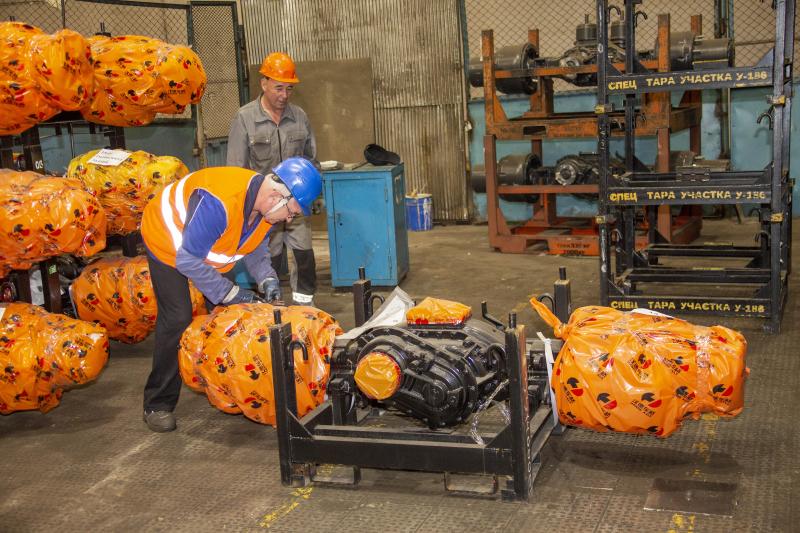
- Каким был бы идеальный результат? Существует некая целевая планка?
– Мы хотим так настроить поставки в цеха, чтобы и оборудование не простаивало, и лишних запасов не скапливалось. Кроме того, автоматизация планирования должна избавить персонал от масштабных инвентаризаций, потому что все заготовки - полученные, переданные в цех, использованные в производстве, - регистрируются в системе без промедления. На обстановке в цеху нововведение уже сказывается: тары стало меньше, около 30 квадратных метров высвободилось. Это, во-первых, комфорт работы для операторов, наладчиков и сборщиков, а во-вторых, снижение травмоопасности. Конечной целью мы видим сквозное планирование поставок для всех подразделений технологической цепочки.
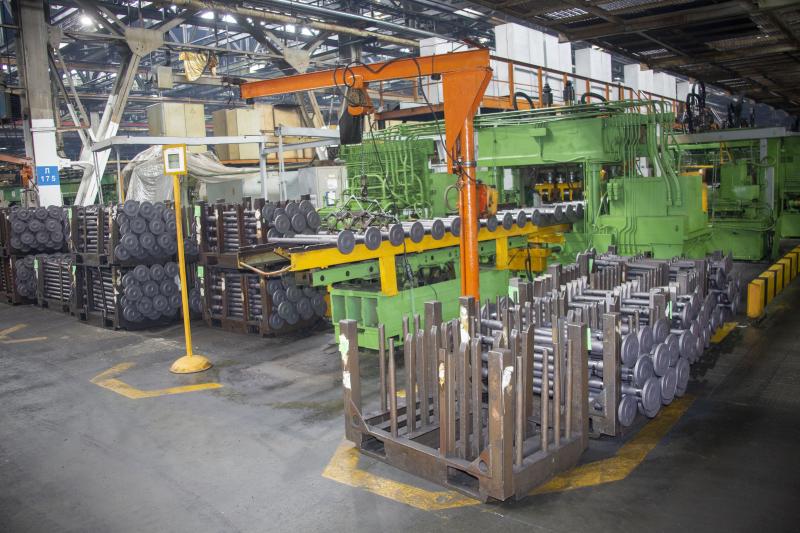
– Когда проект выйдет за пределы пилотного цеха?
– В августе. Мы уже модернизировали склад №58934, заканчиваем переводить на стеллажное хранение склад № 58960. С ними задача усложняется, потому что на них хранятся заготовки и комплектующие для нескольких цехов агрегатного производства. Одновременно начнем вводить автоматизированное планирование для завода двигателей. Чем активнее мы будем внедрять эти механизмы, тем тоньше сможем настраивать логистические процессы под потребности разных подразделений. Тем эффективнее будет и их работа.
Текст: Татьяна Белоножкина
Фото: Виталий Зудин
если SAP уйдет из России
Ответить (0)